Plastikflasche an Roboter: „Befüllen Sie mich bitte mit der blauen Seife.“ Roboter an Plastikflasche: „Verstanden!“ Einer der Einfüllhähne des Roboters schwenkt zum Standplatz der Flasche, richtet sich millimetergenau ein und fährt seinen Füllstutzen in ihren Hals. Blaue Seifenlauge fließt in die Flasche, bei Dreiviertel-Füllung ist Schluss. Plastikflasche an Roboter: „Füllvorgang erfolgreich abgeschlossen. Verschlussvorgang starten. Verschlussfarbe Weiß.“ „Aye-eye, sir!“ Ein Arm des Roboters nimmt einen weißen Pumpverschluss zwischen seine weich gepolsterten Greifzangen und schraubt sie sanft auf die Flasche. Plastikflasche an Roboter: „Vorgang abgeschlossen. Bitte übergeben Sie mich an die Verpackungs- und Versandeinheit. Danke für Ihre Arbeit!“
Dieses Gespräch zwischen Flasche und Roboter hat so nie stattgefunden. Maschinenkommunikation kennt keine Höflichkeitsfloskeln. Nichtsdestoweniger ist der Prozess exakt so abgelaufen. Die „intelligente“ Plastikflasche hat ihren „Werdegang“ völlig selbstständig gesteuert. Schauplatz dafür ist die Laboranlage „Smart Factory“ in Kaiserslautern. Dort wird, quasi im Minimundus-Format, simuliert, was unter dem Schlagwort „Industrie 4.0“ die industrielle Fertigung nahezu völlig auf den Kopf stellen soll. Kurz: Zentrale Computerintelligenz bzw. -steuerung wird durch dezentrale Produktintelligenz abgelöst. Was das heißt, erklärt Wolfgang Wahlster vom deutschen Forschungsinstitut für künstliche Intelligenz: „Industrie 4.0 ist ein grundlegender Wandel im Denken von Produktionsprozessen. Der Rohling selbst trägt die Informationen, wie er bearbeitet werden will, er kennt seinen Auftraggeber und seinen Zielort.“ Folglich ist die Fabrik der Zukunft nicht starr, sondern modular. Der Anwender kann sie sich wie mit „Legosteinen“ beliebig konfigurieren.
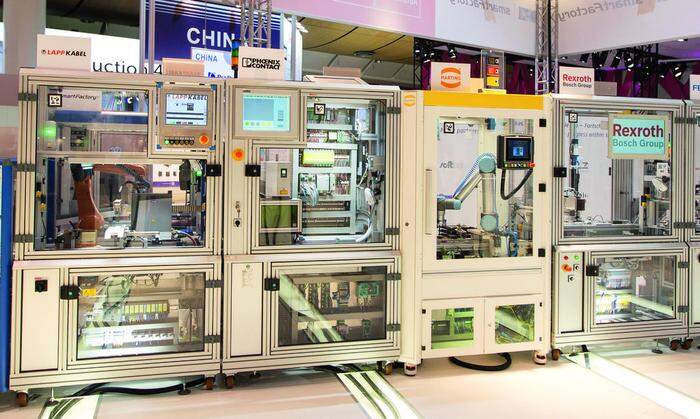
Die Smart Factory, die im Konsortium von 16 Partnern entwickelt und getest wird, kann heute schon auf Messen bestaunt werden (siehe Bild unten). Doch bei aller Euphorie und der respektablen Funktionalität der Demonstrationsanlage gibt es noch viele Fragen zu klären und Probleme zu lösen. Prof. Dr. Detlef Zühlke ist der Initiator der Smart Factory und deren Vorstandsvorsitzender: „Es fehlen noch wesentliche einheitliche Standards, die eine breite Interoperabilität ermöglichen. Auch Security- und Safety-Themen sind noch nicht ausreichend entwickelt, um bestehende Zweifel bei den Anwendern auszuräumen. Nicht zuletzt sind auch noch etliche rechtliche Fragen zu klären – beispielsweise die nach dem Eigentümer der gesammelten Datenmengen“.
Und Letzteres ist gewiss eine entscheidende Frage. Schließlich werden bei der realen Industrie 4.0 heute noch unvorstellbare Datenmengen – so genannte Big Data – generiert werden. Denn sie durchdringen nicht nur Fertigungshallen, sondern gesamte Fabriken, nein, ganze Wertschöpfungsketten.
Ein Funketikett als „Gehirn“ der Flasche.
Unsere „intelligente“ Plastikflasche hat in ihrer Wertschöpfungskette über ein langes Förderband nun den Bereich Verpackungs- und Versandlogistik erreicht. Die Frage, woher die Flasche nun ihre „Intelligenz“ nimmt, ist leicht beantwortet: Auf ihr klebt ein RFID-Etikett – auch „Funketikett“ genannt – das quasi ihren genetischen Code enthält. Aus diesem lesen u. a. der Füllroboter, die Verpackungsmaschine und zuletzt die Transportlogistik alle für sie notwendigen Informationen aus. Das Etikett trägt die Flasche während ihres gesamten Lebenszyklus an sich. Sie steuert sich damit bis zu ihrem Empfänger. Plastikflasche an Tranportlogistik: „Bitte integrieren Sie mich in die Lieferkette für Seifenflaschen mit einem weißen Verschluss!“ Die Software, die das liest, weiß, dass Flaschen mit einem weißen Verschluss genau einem Empfänger zugeordnet sind und setzt die entsprechenden Prozesse in Gang. Hat die Flasche ihren Empfänger bzw. Auftraggeber erreicht, ist ihr gesamter Entstehungs- und Transportweg lückenlos dokumentiert.
Und wo bleibt der Mensch?
Hinter all diesen Prozessen stecken extrem komplexe Software-Applikationen. Diese unterstützen den Menschen, treffen aber auch selbstständig Entscheidungen. Steckt darin der Ansatz, dass der Mensch selbst von seinen Maschinen ersetzt wird? Prof. Zühlke sieht diese Gefahr nicht: „Der Mensch ist und bleibt der wichtigste Akteur und Erfolgsfaktor im Umfeld der smarten Fabrik – auch wenn sich die Aufgabenfelder und Tätigkeiten für die Arbeitnehmer von Morgen ändern werden. Immer mehr Interdisziplinarität wird gefragt sein. Nehmen Sie beispielsweise einen Instandhalter in der Produktion. Sein Aufgabenspektrum wird sich wahrscheinlich um die Wartung von Softwarekomponenten erweitern.“
In der realen Fabrik ist die Industrie 4.0 heute nur in Teilbereichen umgesetzt, beispielsweise mittels RFID-Werkstückidentifikation zur Anlagensteuerung. Experten sind aber überzeugt, dass wir schon bald große Schritte in die neue Industriewelt erleben werden.